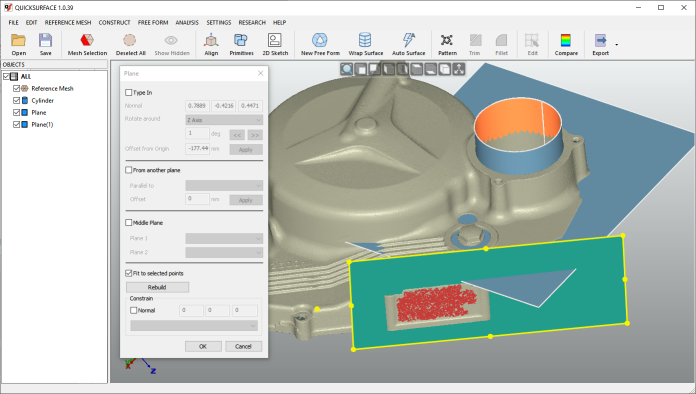
ave you ever wondered how you can use 3D scanning to redesign a part that was damaged or worn out? Or you need it to be similar, but with minor adjustments ? In that case you need a 3D Reverse engineering solution. Reverse Engineering is a powerful way to create digital designs from a physical part.

With the new technologies it is easy. You can use every 3D scanner to scan your object and then use QUICKSURFACE software to create a 3D model (CAD model). This process is called 3D Reverse Engineering.
3D reverse engineering is the process of extracting design intent from an existing physical object by creating a 3D CAD model of the object. Reverse engineering is a commonly used technique for situations where there is no access to CAD data, dimensional information, or drawings of machined parts that have been discontinued and are no longer accessible.
Once the 3D model is created, it can be used to analyse the object, make modifications, or recreate it using 3D printing or other manufacturing methods.
Why do we need 3D reverse engineering ?
- Create producible designs
- Edit and repair CAD data for broken tools and molds
- Increase design capabilities
- Use existing assets to reverse engineer new parts
- Transform physical parts into CAD for new designs
- Create new parts to fit with existing parts
- Simplify models for simulation
- Prepare models for manufacturing
- Speed up your time for manufacturing
- Reduce costs for design
How does the process from SCAN to CAD work?
3D Reverse engineering can be a complex and tedious job, sometimes a time-consuming process to achieve the required results while maintaining accuracy and design intent. With QUCKSURFACE software you can save time and money redesigning your products in a few quick and easy steps.

Import any mesh data (OBJ, STL or PLY) from scan.

2. Extract & create primitives
Extract features (planes, cylinders, spheres, free form patches, revolved and extruded surface…) and create primitives.

Position the object into the world coordinate system.

Create complex Hybrid 3D models for both organic and prismatic shapes.

Create 2D Sketches for Revolved and Extruded surfaces.

Use advanced tools for Trimming & Boolean, Loft, Sweep surfacing and Create fillets.

Compare the CAD model against the reference mesh at any time of your process to maintain the accuracy.

8. Export to other CAD Packages or use it for 3D printing
Export the results in industry standard file formats like IGES or STEP for use in other CAD packages.
In conclusion – why do we need 3D Reverse Engineering?
3D reverse engineering finds applications in various industries such as manufacturing, automotive, aerospace, and product design. It is particularly useful when dealing with legacy parts, antique objects, or situations where the original design documentation is unavailable. By creating a digital representation of existing objects, engineers and designers can make modifications, improvements, or reproductions based on the captured data. QUICKSURFACE is the most cost-effective 3D reverse engineering solution available, that ensures users get the best results at an affordable price.
Original post can be found on the Quicksurface website
https://www.quicksurface.com/general-3d-reverse-engineering-quicksurface/3d-reverse-engineering/what-is-3d-reverse-engineering/