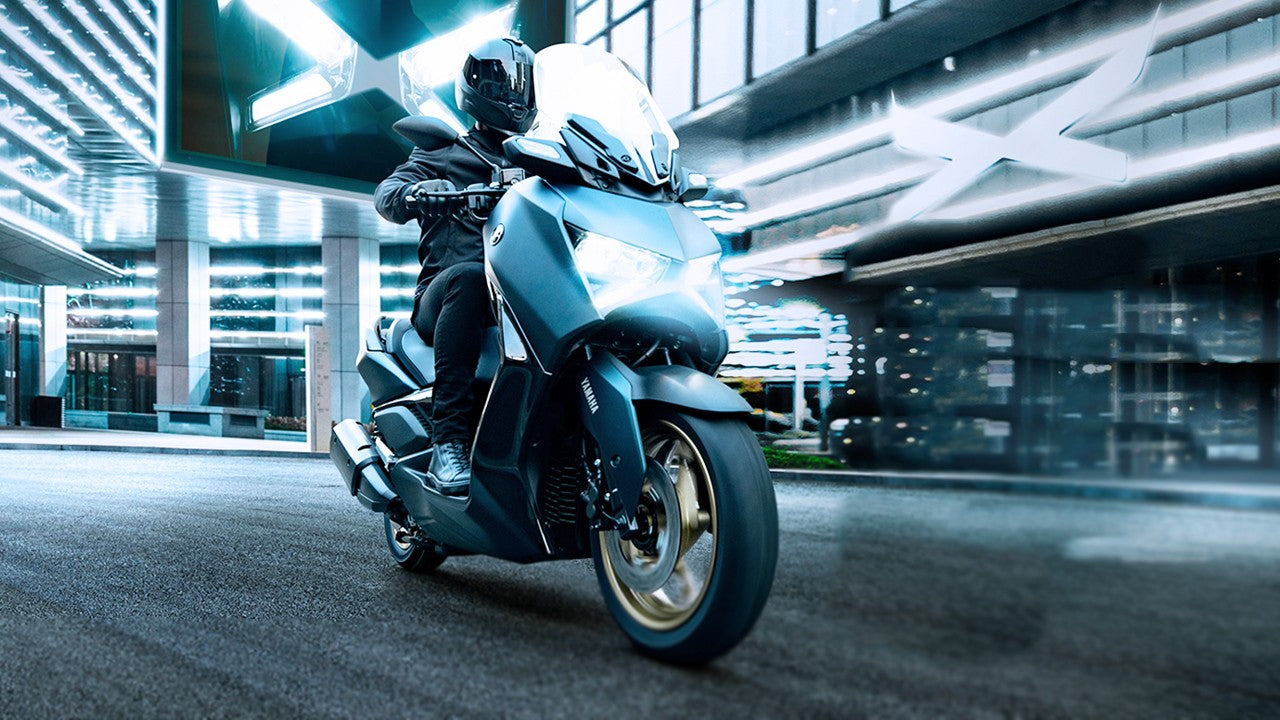
The motorcycle industry is a dynamic and rapidly evolving sector, known for its constant push towards innovation and precision engineering. As motorcycles become more sophisticated, the need for stringent quality control and accurate measurement of components has never been greater. Manufacturers must ensure that every part, from individual components to the complete assembly, meets the highest standards of accuracy and quality to guarantee performance, safety, and customer satisfaction.
Scantech provides advanced 3D scanning solutions to address these critical needs. In the following case study, we will explore how our client utilized Scantech’s 3D scanning technology to overcome their measurement challenges and achieve superior quality control in their manufacturing process.
Case Background
Our client, Incolmotos Yamaha, is a leading manufacturing and distribution company in the automotive sector. With over 45 years of experience in motorcycle sales and distribution, they are well-known for offering high-quality products in the Colombian and Latin American markets. Precision in the manufacturing process is crucial for Incolmotos Yamaha to maintain their reputation for excellence.
The client needed to perform precise GD&T measurements on components with different sizes, geometries and surface finishes to ensure that they meet specification standards. Additionally, they needed to measure the installation positions of critical components like motorcycle frames, engines, tires, and brake systems to ensure that they fit together perfectly during assembly.
To ensure these components meet their rigorous standards, the company needed an accurate and reliable method to 3D scan motorcycle parts and measure both individual parts and the assembled motorcycle. The acquired 3D data can be used for assembly analysis such as fixture analysis, gap & interference analysis to ensure the high quality of the whole vehicle.
Traditional Methods and Challenges
Incolmotos Yamaha initially relied on traditional measurement methods to ensure the precision of their components and assemblies, but several significant challenges are presented:
- Data Inconsistency: Different operators using manual tools could produce varying results, leading to inconsistencies in the measurement data. This inconsistency made it difficult to ensure uniform quality across all components and assemblies.
- Lack of Standardization: Traditional methods often lacked standardization in the measurement processes, leading to variations in data collection and interpretation. This lack of standardization hindered the ability to maintain consistent quality across different production batches and manufacturing sites.
- High Labor Costs: The reliance on manual measurement methods required skilled labor, which added to the overall production costs. Additionally, the potential for human error increased the likelihood of rework and scrap, further driving up expenses.
- Inefficiency: The overall inefficiency of traditional measurement methods hampered production speed and throughput. With long measurement cycles and frequent rework due to inaccuracies, the entire manufacturing process slowed down, affecting the company's ability to meet market demands promptly.
These challenges underscored the need for a more efficient, accurate, and standardized measurement solution. Recognizing these limitations, Incolmotos Yamaha sought out Scantech's advanced 3D scanning technology to overcome these obstacles and elevate their manufacturing precision and quality control processes.
Project Challenges
Implementing an advanced 3D scanning solution presented its own set of challenges:
- Variability in Parts: Some of its parts are sourced parts from various suppliers, each with its own manufacturing standards. This variability in parts required a versatile scanning solution capable of adapting to different shapes, sizes, and materials without compromising on accuracy.
- Complex Geometries: Many motorcycle components, such as frames and engines, feature complex geometries with intricate details and hard-to-reach areas. Traditional methods struggled to capture these details accurately, necessitating a more advanced approach to scanning and measurement.
- Precision Requirements: High precision was crucial for ensuring the proper fit and function of components in the final assembly. Achieving the required level of accuracy was a significant challenge, especially given the limitations of traditional measurement tools.
Solution and Advantages
By addressing these challenges, Incolmotos Yamaha aimed to leverage Scantech's SIMSCAN 3D scanner and ScanViewer software to improve the precision, efficiency, and standardization of their measurement processes. This strategic move was essential for maintaining their high standards of quality and meeting the increasing demands of the market.
Versatility and Efficiency
The SIMSCAN 3D scanner, being lightweight and portable, is suitable for various work environments. It captures high-resolution surface details with a maximum accuracy of 0.02 mm and an ultra-high scanning rate of 2.8 million measurements per second.
Adaptability to Various Materials
SIMSCAN's blue laser scanning technology handles a variety of materials, including metals and plastics, ensuring clear and accurate results regardless of material complexity.
Excellent for Narrow Spaces
Compared to conventional 3D scanners, SIMSCAN boasts a more compact design and a shorter camera distance. Its steeper view angle allows it to measure hard-to-reach areas and narrow spaces effectively. This capability ensures precise fitting of internal intricate components, such as cylinders and pistons, during engine assembly.
Comprehensive Analysis and Data Management
The ScanViewer software provides powerful tools for detailed inspection and comparison against CAD models. It facilitates efficient data storage, processing, and analysis, streamlining the quality control process and detecting dimensional deviations.
Cost Savings and Enhanced Quality Control
By minimizing reliance on manual methods and reducing rework, Incolmotos Yamaha lowers labor costs and production expenses. The detailed 3D data allows for thorough inspection, ensuring high standards for safe and reliable motorcycles.
The implementation of Scantech's SIMSCAN handheld 3D scanner and ScanViewer software has significantly enhanced Incolmotos Yamaha's measurement accuracy and efficiency. John Jader Morales, Metrology Leader at Incolmotos Yamaha, notes that the technology effectively handles complex geometries and diverse materials, ensuring high production standards.
Scantech provides extensive applications of 3D scanning technology in the motorcycle industry, including quality control, reverse engineering, and R&D solutions. Dedicated to continuous improvement, Scantech supports clients in their digital transformation journey, ensuring they stay at the forefront of technological advancements. This commitment allows clients to achieve greater precision and efficiency in their processes, maintaining a competitive edge in the industry.