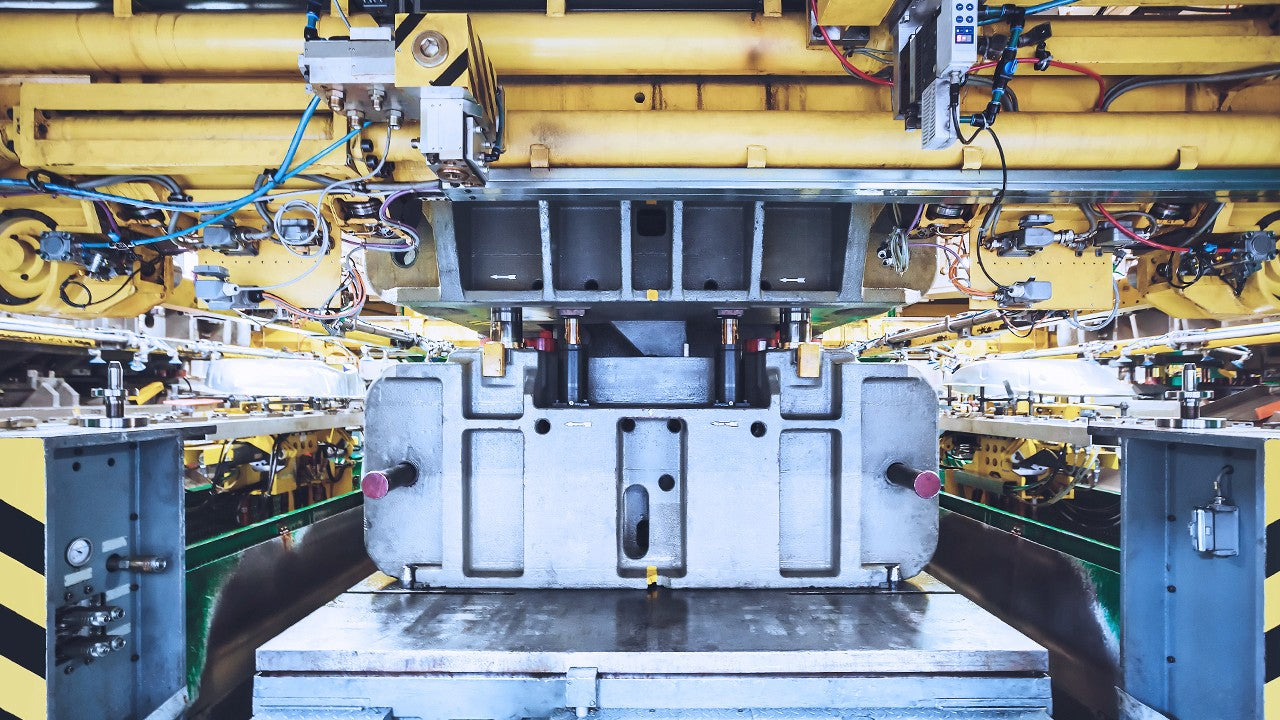
The production of automotive parts relies heavily on molds and dies, which must be manufactured to exact specifications to ensure the integrity and performance of the final product.
The process of developing molds and dies for major body panels involves several critical steps. These include die design, pattern development, casting, construction, and tryout. Among these, the construction phase stands out as the most costly and time-consuming.
Traditional inspection methods, while effective to an extent, often fall short in capturing the minute details and complex geometries of these tools. This is where 3D scanning can help to enhance the inspection process. By employing high-precision 3D scanning for automotive mold and die inspection, manufacturers can achieve high accuracy, efficiency, and reliability.
This article shed lights on how 3D scanning can help to improve automotive die inspection, exploring how it enhances quality control, reduces downtime, and drives innovation in the automotive manufacturing sector.
Challenges of Measuring Molds and Dies
- Size and Mobility: Automotive molds and dies are large, therefore, it is hard to transport them to dedicated measurement rooms.
- Complex Geometries: Molds feature intricate surfaces with undercuts, sharp edges, deep cavities, and fine details. Traditional methods struggle to capture such complexity accurately.
- Reflective Surfaces: The measurement of metallic molds may result in measurement noise due to their reflective nature.
Significance of Measuring Molds and Dies
Thorough inspection is essential to ensure that the molds and dies align with the original design. Errors resulting from machining not only affect the die assembly but also impact the die’s ability to create acceptable panels during tryout. If any dimensional errors are detected during assembly or tryout, it can significantly delay the delivery of the complete die to production by several days or even weeks.
When an error is identified, construction is halted, and an extensive root cause analysis begins. To prevent delays caused by process errors, precise inspection of die is crucial.
Measure a Die to Assess Dimensions, Flatness and Defects
For this project, our client needed to inspect a die used in the production of automotive stamping parts. The goal was to assess geometric dimensions, flatness, and identify any defects.
- Challenges
Due to the die’s large size and weight, it is inconvenient to move it. It is necessary to measure it right on the shop floor.
The die has intricate features, including curved surfaces, holes, concave-convex areas, and sharp corners. Moreover, there are obstructions and blind spots that conventional measuring tools struggle to handle.
Additionally, the reflective surface of the mold could potentially interfere with 3D laser scanning, affecting measurement accuracy and precision. It’s worth noting that the customer has specified no powder coating or target sticking.
- 3D Scanner: TrackScan-Sharp
TrackScan-Sharp optical 3D measurement system was used to capture the physical geometry of the molds. It brings optical measurement to a whole new level by offering a tracking distance of up to 6 meters, a volumetric range of 49 m3, and volumetric accuracy of up to 0.049 mm (10.4 m3).
- Workflow
Laser Scanning: The 3D scanner captured the mold’s surface, creating a point cloud representation on a computer.
Data Generation: Import the scanned point cloud data into computer software for processing. Next, perform alignment, registration, and other necessary operations to convert it into STL data.
Deviation Analysis: By comparing the scanned data with the original CAD model, we identified any deviations from the design specifications. This analysis guided subsequent steps.
Benefits
On-Site Measurement Process: The entire measurement process occurred on-site within the workshop, as TrackScan-Sharp is portable and resistant to vibrations.
Powder-Free and Target-less Measurement: Thanks to its optical tracking and advanced algorithm, TrackScan-Sharp eliminated the need for powder spraying or attaching targets to the objects being measured.
Efficient Workflow: Leveraging its impressive 49-m3 measurement volume and high measurement rate, the 3D scanner ensured an efficient process. From initial scanning to the final inspection report generation, the entire cycle was completed in a remarkably short time—just 40 minutes.
Inspection of Large-scale Molds
- Project Objective
The primary objective of this project is to perform a comprehensive inspection of car roof die using the advanced KSCAN-Magic 3D laser scanner. The aim is to detect any deviations or defects, and improve the overall manufacturing process efficiency.
- Challenge of Inspection Large-scale Die
Size and Complexity: The die features a large size and intricate details that are difficult to measure with traditional tools.
Precision Requirements: Automotive parts require high precision to ensure proper fit and function, necessitating highly accurate measurement tools.
Data Management: The vast amount of data generated during inspection needs to be processed and analyzed efficiently to provide actionable insights.
- 3D Scanner: KSCAN-Magic
The KSCAN-Magic 3D scanner excels in capturing detailed 3D data with high accuracy of up to 0.020 mm. It is highly versatile, suitable for scanning objects of various sizes and materials. With its high scanning speed, it enables quick data collection, while its user-friendly interface and portability make it suitable for use in various environments.
- Workflow
Data Collection: Scan the entire surface of the car roof die, capturing detailed 3D data. The scanner's high precision and speed allow for quick and accurate data collection, even for large and complex dies.
Data Processing: Use the accompanying software to process the 3D data. The software aligns and merges the scanned data into a complete 3D model.
Analysis: Compare the scanned 3D data with the original CAD design to identify any deviations or defects. The software provides detailed reports on dimensional accuracy, surface quality, and other critical parameters.
- Benefits
Ease of Use: The user-friendly nature of the KSCAN-Magic allows operators to quickly learn and efficiently perform inspections.
Efficiency: The fast scanning speed of up to reduces inspection times, helping to maintain production schedules.
High Accuracy: The high precision of the KSCAN-Magic ensures accurate inspection of even the smallest defects or deviations with an accuracy of up to 0.020 mm. KSCAN-Magic featured a built-in photogrammetry system, enhancing the accuracy and stability of measurements. This minimized errors and rework due to scan misalignment.
Flexible Operation: The 3D scanner scanned the die from various angles and distances, unaffected by workshop vibrations. It was also portable and lightweight, making it easy to carry on business trips.
Real-time Reporting: The professional scanning software generated color maps showing deviations by comparing the 3D data with the original CAD model.
Scantech 3D https://www.linkedin.com/pulse/3d-digital-solutions-automotive-mold-die-inspection-3dscantech-vnmxc/
Conclusion
The implementation of 3D scanning technology for mold and die inspection in automotive manufacturing significantly enhances production efficiency, quality control, and cost savings. By utilizing advanced 3D scanners like TrackScan-Sharp and KSCAN-Magic, companies can achieve precise, real-time, and comprehensive inspection results, ensuring that their molds and dies meet the highest standards of quality and precision.